sheet metal article The blanking process is classical elasto-plastic large deformation. As Fig. 1 . $17.79
0 · which thickness called sheet metal
1 · types of sheet metal material
2 · types of sheet metal fabrication
3 · metal sheet thickness in mm
4 · maximum thickness of sheet metal
5 · disadvantages of sheet metal
6 · different types of sheet metals
7 · characteristics of sheet metal
Buy ZINUS Quick Lock Metal Smart Box Spring, 4 Inch Mattress Foundation, Strong Metal Structure, Easy Assembly, King, White: Box Springs - Amazon.com FREE DELIVERY possible on eligible purchases
This paper aims at scattering light on the recent research and developments in the sheet metal forming processes over the last two decades. Most of the literature available on .
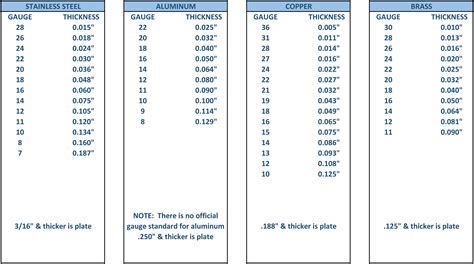
cnc spray machine
The sheet metal industry has seen more technological advances than any other .The blanking process is classical elasto-plastic large deformation. As Fig. 1 .The geometry of the blanking process modelled in this study is presented in .

which thickness called sheet metal
Optimization of process parameters in sheet metal forming is an important task to .Sheet Metal. In subject area: Engineering. Continuous folding technique is a .
Sheet metal is metal formed into thin, flat pieces, usually by an industrial process. Thicknesses can vary significantly; extremely thin sheets are considered foil or leaf, and pieces thicker than 6 mm (0.25 in) are considered plate, such as plate steel, a class of structural steel. Sheet metal is available in flat pieces or coiled strips. The coils are formed by .Sheet Metal. In subject area: Engineering. Continuous folding technique is a technique wherein the metal sheet is pre-folded by passing it through a set of sequential and circumferential .The manufacturing & design guide. Learn how to effectively design sheet metal parts. This guide starts with the basics and moves toward design best practices and advice on material . Uncover the secrets of sheet metal: materials, geometries, and processes. Explore the world of stainless steel, carbon steel, and aluminum.
types of sheet metal material
types of sheet metal fabrication
Sheet metal is metal formed into thin, flat pieces, usually by an industrial process. Thicknesses can vary significantly; extremely thin sheets are considered foil or leaf, and pieces thicker than 6 mm (0.25 in) are considered plate, such as .

We would like to draw your attention to this Special Issue of JMMP on “Analysis and Modelling of Sheet Metal Forming Processes”. Analysis and modeling play a vital role for accessing the feasibility of sheet metal forming processes. Nowadays, almost no tool design in industrial stamping is manufactured without successful virtual tryout.
NX12 has been a well-received release from Sheet Metal users. This is the sixth article in a series highlighting what’s new. Convert to Sheet Metal is a valuable command when importing models from other CAD systems, neutral file .
A Beginner’s Guide to Swaging Machines: Perfecting Sheet Metal Shaping and Forming. In the realm of metalworking, where precision and artistry intertwine, the swaging machine emerges as an indispensable tool for shaping and forming sheet metal. For those embarking on this enthralling journey, this article serves as an illuminating guide . In this manuscript, we present a comprehensive overview of true digital twin applications within the manufacturing industry, specifically delving into advancements in sheet metal forming. A true digital twin is a virtual representation of a physical process or production system, enabling bidirectional data exchange between the physical and digital domains and . The sheet metal industry has seen more technological advances than any other since the last century. Right from hand-forming processes to finite element based simulation, the transformation is very significant. They have prominent industrial applications especially in automotive industries. This may be attributed to the ease with which the .In this article alone, fourteen types of sheet metal fabrication are mentioned. These varying techniques allow make it possible to create relatively complex parts by cutting flat sheets, bending parts into place and adding holes, slots, and notches cut in all the right places.
At last, Metal-Interface unites the sheet metal industry across several countries with complementary services: news, adverts, job offers and knowledge sharing via a sheet metal wiki. For all questions, do not hesitate to contact us: Metal-interface.com, the leading website created by and for professionals in the field of sheet metal forming, in . Conventions of sheet-metal part drawing The conventions for sheet-metal part drawing are as follows: solid lines represent the boundaries of the part and the dotted lines or dashed lines represent [~ Punch-hoSder ! 2 $ 4 Fig. 1. Bending operation. ( Design and manufacturing of sheet-metal parts C.-H. WANG and D. A. BOURNE 283 Fig. 2.
Sheet metal screw size conversion. Sheet metal screws are used with metallic and non-metallic materials that are too thin to tap. They are also used when rear access is obstructed, preventing the installation of a nut. Sheet metal screws are typically reusable, one-piece, high-strength fasteners that can be removed for maintenance and repair. . Sheetmetal is simply any metal alloy that stores as a sheet, or is coiled as a matter of convenience to ease handling–some coils stretch for more than a mile. Although no firm break exists between categories, for most alloys, sheet thickness ranges from 0.2 to 6 mm. Plate refers to thicker material, while foil denotes thinner (Fig. 1).
Convert to Sheet Metal. The Convert to Sheet Metal tool uses a pre-existing file to quickly make a parametric and native Alibre Design sheet metal part based on the geometry of a pre-existing. Once a part has been selected, a planar face is selected for the initial tab. Flanges are created by selecting the edges of the part that are shown in the Bends section.A comparison of traditional and modern forming methods is presented here in an attempt to illustrate the evolution of different incremental sheet metal forming techniques. Emphasis is placed on conventional spinning, shear forming and modern computer-controlled forming methods that are currently being studied.Related Articles. Sheet Metal: Convert to Sheet Metal. Number of Views 1.71K. Setting thickness and bend radius for a Sheet Metal part. Number of Views 2.96K. Sheet Metal: Material and Bend Table Improvements. Number of Views 1.29K. How to unfold a .
As such, this article explores the world of galvanized sheet metal, covering its definition, differences from non-galvanized alternatives, and the various galvanization types. In addition, it will provide a guide on how to galvanize sheet metal and detail the advantages and diverse applications of this versatile material.
metal sheet thickness in mm
However, during sheet metal forming, tools contact undeformed sheet in every case. In this article I’ll focus on the strip-draw test. During a strip-draw test, clamping force (F c) is adjusted using a screw, or with a hydraulic system. Then the test apparatus pulls the sheet at constant speed as researchers record the pulling force (F p). In . Lift a sheet metal from the storage rack and place it on the lift table cart jack. Pull and slide the sheet metal from the storage rack and lean on the trolley-lifter. 2 (transport the sheet metal from the storage rack to laser cutting machine) The other end of the sheet metal needs to be supported manually (by a leader) while pushing. The sheet metal fabrication industry is undergoing a profound transformation, driven by technological advancements, sustainability concerns, and changing market demands. This article explores the future of sheet metal fabrication, highlighting key trends and forecasts that are shaping the industry’s evolution. Sheet metal machines are widely used in various manufacturing industries for shaping, cutting, and forming sheet metal into different components. Some of the industries that extensively utilize sheet metal machines include light industries such as electrical and medical equipment, all the way up to heavy industries such as automotive, rail, oil and gas, as well as .
Explore the latest full-text research PDFs, articles, conference papers, preprints and more on SHEET METAL FORMING. Find methods information, sources, references or conduct a literature review on .
Sheet metal drawings serve as the foundation for sheet metal engineers to conduct sheet metal fabrication, aiding them in accurately understanding the structure and requirements of the part, thus enabling precise fabrication. Sheet metal drawing is a manufacturing process used to form flat sheet metal into a desired shape using a die and a . This article focused on seven of the most common mistakes in sheet metal bending, providing provide practical tips to avoid them. By incorporating proper bend relief, calculating bend allowance accurately, and ensuring adequate support across flanges, you can be sure your parts will transition seamlessly from CAD, through our app , and into . This is the 40 sheet metal article (I mentioned earlier) posted by "KUBE" on Fordbarn 12/30/07 at 4:20PM. His words are in quotes. "I POSTED THIS IN MARCH 2004. HOPE IT HELPS. "I received so many requests for tips on aligning the front sheet metal on '40s I was knocked to the floor! We all know that the factory alignment was usually quite poor.
Introduction. Sheet metal manufacturing is a fundamental part of modern industry, transforming raw metal into essential components for a wide range of products, from consumer electronics to heavy machinery. This precision-driven process transforms flat metal sheets into intricate components. Over the decades, sheet metal manufacturing has evolved from manual .Explore the latest full-text research PDFs, articles, conference papers, preprints and more on SHEET METAL. Find methods information, sources, references or conduct a literature review on SHEET METALEffective July 2023, the Annual Physical Incentive form is no longer required. - Traditional tolerance analyses such as the worst case methods and the statistical methods are applicable to rigid body assemblies. However, for flexible sheet metal assemblies, the traditional methods are not adequate: the components can deform, changing the dimensions during assembly. This paper evaluates the effects of deformation on component tolerances .
maximum thickness of sheet metal
Shop easy to assemble box springs all expertly packed and shipped to your door. Don't forget to pair your box spring with one of our highly rated mattresses for the perfect snooze available in twin, full, queen, king, and cal king sizes.
sheet metal article|types of sheet metal material